Конструктивные способы повышения жесткости
Основные задачи курса Сопротивление материалов представляет собой один из разделов механики твердого деформируемого тела, который является наукой об инженерных методах расчета на прочность, жесткость и устойчивость элементов машин, сооружений и других конструкций. Под прочностью понимается способность конструкции, ее элементов сопротивляться разрушению при действии эксплуатационных нагрузок. Расчет на прочность является первой и основной задачей курса "Сопротивление материалов ”. В результате решения этой задачи определяются размеры элементов конструкций, исключающие возможность их разрушения при реальных нагрузках. Второй задачей является расчет конструкции и ее элементов на жесткость. Под жесткостью понимают способность конструкции и ее элементов сопротивляться деформациям, т. е. изменению их форм и размеров. Жесткость считается обеспеченной, если деформации не превосходят заданных величин, допустимых при эксплуатации конструкции. Под устойчивостью понимается способность конструкции и ее элементов сохранять или первоначальную форму упругого равновесия при действии нагрузки или восстанавливать ее после снятия нагрузки, так, при сжатии длинного прямого стержня осевой нагрузкой, приложенной на конце стержня, последний вначале остается прямым, т. е. прямолинейная форма стержня является устойчивой. При достижении нагрузкой некоторой критической величины стержень искривляется, выпучивается в сторону или, как принято говорить, теряет устойчивость. Другой пример: известная Останкинская телевизионная башня, ее ось направлена строго по радиусу земли. Однако при действии ветровых нагрузок, имеющих сложный характер, верхний конец отклоняется от исходного положения, примерно, на три с половиной метра, т. е. ось искривляется. После снятия внешних воздействий форма равновесия восстанавливается, таким образом, данная конструкция устойчивая. Кроме обеспечения прочности, жесткости и устойчивости конструкция должна быть экономичной, т. е. размеры конструкции и ее элементов должны быть такие, чтобы материал, из которого они изготовлены, исчерпывался полностью с точки зрения нагружения, иначе конструкция будет иметь неоправданно большую массу, габариты. Для выполнения указанных требований необходимо придать элементам конструкции наиболее рациональную форму и, учитывая свойства материалов, из которых они будут изготавливаться, определить размеры в зависимости от величины и характера нагрузок. Иначе говоря, машины, сооружения, любые конструкции должны быть легкими, дешевыми и вместе с этим надежными, т. е. работать без риска поломки или опасного изменения формы и размеров весь период эксплуатации. Сопротивление материалов основывается на теоретическую механику, физику, материаловедение и вместе с этим как наука является базой для 5 таких дисциплин, как строительная механика стержневых систем, теория упругости, теория прочности, детали машин и смежных дисциплин. В сопротивлении материалов для упрощения расчетов вводят ряд допущений: Допущения в геометрии тел. Прежде всего многообразие элементов конструкций, исчисляемых тысячами, сводят к трем категориям тел, которые и являются объектами расчета на прочность, жесткость и устойчивость. К ним относят стержни, пластины, оболочки, массивы. Стержень или брус – это тело, у которого один размер (длина) во много раз превышает два других (поперечных) размера (рис. В.1,а) Размеры (H,B)l. Рис. В.1 В машинах и сооружениях встречаются стержни прямолинейные (рис. В.1,б) (у которых ось является прямой линией), а также криволинейные (рис. В.1,г). Примером криволинейных стержней могут служить грузоподъемные крюки, звенья цепей и др. Стержни, у которых толщина стенки значительно меньше габаритных размеров поперечного сечения, называются тонкостенными (рис. В.1,в). В настоящее время они широко применяются в строительных конструкциях, судостроении и особенно в авиастроении. Пластинка – тело, у которого два размера значительно больше третьего (рис. В.2,а) 6 Рис. В..2 К пластинкам могут быть отнесены фундаментные плиты (рис. В.2,а), железобетонные междуэтажные перекрытия, плоские днища и крышки резервуаров и цилиндров, диски турбомашин. Оболочкой называется искривленная пластинка, т.е. тело, ограниченное двумя криволинейными поверхностями, расстояние между которыми (толщина оболочки) мало по сравнению с его другими размерами (рис. В.2,в). К оболочкам относят неплоские стенки тонкостенных резервуаров, котлов, купола зданий. Оболочки могут быть цилиндрические, конические, сферические, комбинированные и т.д. Массив – это тела у которых размеры одного и того же порядка. К ним относят фундаменты сооружений (рис. В.2,б), подпорные стенки, основания ряда тяжелого оборудования и т.д. Допущения, вводимее в свойство материала. Разнообразие структуры и физико-механических свойств реального тела крайне усложняет его исследование. Поэтому сопротивление материалов прибегает к схематизации свойств материалов и пользуется рядом допущений, облегчающих решение вопросов инженерной практики с известной степенью приближения к действительности. К числу таких основных допущений относятся: 1. Допущение об однородности и непрерывности материала. В сопротивлении материалов вместо реального тела рассматривается однородное тело, свойства которого не зависят от его объема. При этом предполагается, что физико- механические свойства тела во всех его точках одинаковы и материал равномерно без пустот заполняет весь объем тела. Это допущение вполне приемлемо для таких материалов, как сталь, медь, чугун и т. д., и менее приемлемо для кирпича, бетона, древесины и других строительных материалов. 7 Однородные тела, у которых физико-механические свойства одинаковы во всех направлениях, называются изотропными (литая сталь, литая медь, стекло, хорошо приготовленный бетон и т. д.). Материалы, имеющие одинаковые физико-механические свойства только для определенных направлений волокон, расположенных параллельно осям какой-либо одной прямоугольной системы координат, называются ортотропными (прокатная сталь, котельное железо, стальная проволока, отчасти прямослойная древесина без сучков). Материалы, не обладающие свойствами изотропности и ортотропности, называются анизтропными (косослойная древесина, стальная проволока, закрученная в холодном состоянии и т. д.). В сопротивлении материалов обычно рассматриваются только изотропные и ортотропные материалы. 2. Деформации малы по сравнению с размерами деформируемого тела. При этом считают, что соблюдается закон Гука. При расчетах пренебрегают изменениями в расположении внешних сил относительно отдельных частей тела при деформациях. Уравнения статики составляют для недеформированного тела. В некоторых случаях от этого принципа приходится отступать. Малые деформации рассматриваются как бесконечно малые величины в математическом анализе. Если в каком-либо уравнении есть слагаемые с деформациями в первой степени и слагаемые с их произведениями и более высокими степенями, то последние отбрасывают как величины высшего порядка малости. Допущение о малости деформаций делает возможным применение принципа независимости действия сил. Этот принцип в сопротивлении материалов формулируется следующим образом: результат воздействия на тело системы сил равен сумме результатов на тело тех же сил, приложенных в любой последовательности. Например, на балку действуют силы Р1 и Р2 , которые в сечении К вызывают прогиб уК. Этот прогиб можно найти, как сумму прогиба вначале силой Р2, а затем силой Р1 (рис. В.3), или наоборот. 8 Рис. В.3 Принцип независимости действия сил является основным руководящим принципом при решении подавляющего большинства задач сопротивления материалов. Заметим, что он применим при выполнении закона Гука. 3. Предполагается, что соблюдается гипотеза плоских сечений. При решении большинства задач сопротивления материалов используется гипотеза плоских сечений (Я. Бернулли), на основании которой предполагается, что плоские сечения, приведенные в теле до его деформации, остаются плоскими и перпендикулярными к изогнутой оси тела после деформации.
Понятие о прочности, жесткости и устойчивости. Понятие о расчетной схеме. Основные принципы курса. Напряжения и деформации. Допускаемые напряжения. Основные методы оценки прочности конструкций.
Понятие о прочности, жесткости и устойчивости
Сопротивление материалов – наука, изучающая поведение элементов конструкции (деталей машин или элементов сооружений) при действии внешней нагрузки и устанавливающая условия их нормального функционирования.
Элементы конструкций рассматриваются как твердые деформируемые тела. Тело называется деформируемым, если в результате действия внешних сил изменяются его форма и (или) размеры.
Для выполнения заданных функций элемент конструкции должен быть прочным, жестким и устойчивым. Прочностью называется способность элемента конструкции воспринимать внешнюю нагрузку без разрушения. Жесткость – способность элемента конструкции при действии внешних сил деформироваться в установленных пределах. Устойчивостью называется способность элемента конструкции при действии внешней нагрузки сохранять начальную форму равновесия.
Для выполнения указанных требований элемент конструкции должен быть изготовлен из подходящего материала и иметь определенные размеры, которые находятся в результате прочностных и деформационных расчетов. Задачей сопротивления материалов и является разработка методов расчета элементов конструкций на прочность, жесткость и устойчивость.
Понятие о расчетной схеме
Реальный объект обладает множеством свойств, полный учет которых приводит, как правило, к невозможности его расчета. Поэтому перед расчетом составляется расчетная схема объекта. Расчетная схема получается в результате схематизации (упрощения) свойств, значимых для расчета, и пренебрежения свойствами, оказывающими несущественное влияние. Наиболее важными для расчетов в сопротивлении материалов являются свойства материала, форма объекта и внешняя нагрузка.
Схематизация свойств материала
Материал является сплошным, т.е. непрерывно заполняет весь объем тела.
здесь не принимается во внимание дискретная, атомистическая структура вещества. Это допущение вполне оправдано с практической точки зрения, так как большинство материалов имеет настолько мелкозернистую структуру, что без заметной погрешности можно считать их строение сплошным, непрерывным. Это объясняется тем, что размеры реальных деталей во много раз больше межатомных расстояний. Данное допущение позволяет при выводе расчетных зависимостей использовать математический аппарат непрерывных функций;
Материал является однородным и изотропным, т.е. имеет одинаковые свойства во всех точках и направлениях.
Металлы обладают высокой однородностью, т. е. имеют во всех точках детали практически одинаковые свойства. Менее однородными являются дерево, бетон, камень, пластмассы с наполнителем. Например, бетон содержит в себе в качестве наполнителя небольших размеров камни, гравий, щебень, свойства которых отличаются от свойств цемента. В дереве имеются сучки, свойства которых также сильно отличаются от свойств остальной массы дерева. В пластмассах свойства смолы отличаются от свойств наполнителя.
Исследования показывают, что кристаллы, из которых состоят многие материалы, обладают в различных направлениях различными свойствами. Например, для меди прочность кристаллов в разных направлениях различается более чем в три раза. Однако у материалов, имеющих мелкозернистую структуру, благодаря большому количеству кристаллов, расположенных в беспорядке, свойства в разных направлениях выравниваются и можно считать эти материалы практически изотропными. Для таких материалов, как дерево, железобетон, пластмассы, указанное допущение выполняется лишь приблизительно. Материалы, свойства которых в разных направлениях различны, называются анизотропными;
Материал является упругим, т.е. обладает способностью после разгрузки восстанавливать первоначальные форму и размеры;
Для материала справедлив закон Гука: напряжение в точке прямо пропорционально деформации в этой точке.
Схематизация формы объекта
Конструкции, с которыми приходится встречаться на практике, имеют в большинстве случаев сложную форму, отдельные элементы которых можно свести к следующим простейшим типам:
1. Брус - тело, у которого два размера малы по сравнению с третьим (рис. 1.1а). В частном случае брус может иметь постоянную площадь поперечного сечения и прямолинейную ось. Брус с прямолинейной осью часто называют стержнем. Ось бруса - это линия, соединяющая центры тяжести его поперечных сечений. Плоская фигура, имеющая свой центр тяжести на оси и нормальная к ней, называется поперечным сечением бруса.
Оболочка - тело, ограниченное двумя криволинейными поверхностями, расстояние между которыми мало по сравнению с прочими размерами (рис. 1.1б). Пластинка (частный случай оболочки) - тело, ограниченное двумя плоскими поверхностями, расстояние между которыми мало по сравнению с прочими размерами (рис. 1.1в).
3. Массив - тело, размеры которого во всех направлениях мало отличаются друг от друга (рис. 1.1г).
В курсе «Сопротивление материалов» рассматриваются преимущественно тела, имеющие форму бруса постоянного поперечного сечения, и простейшие системы, состоящие из них.
Схематизация внешней нагрузки
Элемент конструкции может быть нагружен поверхностной или объемной, силовой или моментной нагрузкой. Поверхностная нагрузка действует в каждой точке некоторой части поверхности элемента, а объемная нагрузка – в каждой точке его объема.
Рассмотрим два часто используемых приема схематизации.
Если площадь поверхности А , по которой нагрузка распределена с интенсивность р , во всех направлениях существенно меньше размеров тела, то распределенную по поверхности нагрузку заменяют сосредоточенной силой, т.е. силой, проложенной в точке (рис. 1.2);
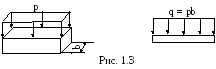
Главные конструктивные способы повышения жесткости без существенного увеличения массы:
- всемерное устранение изгиба, замена его растяжением или сжатием;
- для деталей, работающих на изгиб, целесообразная расстановка опор, исключение невыгодных по жесткости видов нагружения;
- рациональное, не сопровождающееся возрастанием массы, увеличение моментов инерции сечений;
- рациональное усиление ребрами, работающими предпочтительно на сжатие;
- усиление заделочных участков и участков перехода от одного сечения к другому;
- блокирование деформаций введением поперечных и диагональных связей;
- привлечение жесткости смежных деталей;
- для деталей коробчатого типа — применение скорлупчатых, сводчатых, сферических, яйцевидных и тому подобных форм;
- для деталей типа дисков — применение конических, чашечных, сферических форм; рациональное оребрение, гофрирование;
- для деталей типа плит — применение прочных, коробчатых, двутельных, ячеистых и сотовых конструкций.
Замена изгиба растяжением-сжатием
Повышенная жесткость деталей, работающих на растяжение-сжатие, в конечном итоге обусловлена лучшим использованием материала при этом виде нагружения. В случае изгиба и кручения нагружены преимущественно крайние волокна сечения. Предел нагружения наступает, когда напряжения в них достигают опасных значений, тогда как сердцевина остается недогруженной. При растяжении-сжатии напряжения одинаковы по всему сечению; материал используется полностью. Предел нагружения наступает, когда напряжения во всех точках сечения теоретически одновременно достигают опасного значения. Кроме того, при растяжении-сжатии деформации детали пропорциональны первой степени ее длины. В случае же изгиба действие нагрузки зависит от расстояния между плоскостью действия изгибающей силы и опасным сечением; деформации здесь пропорциональны третьей степени длины.
Сравним консольную балку круглого сечения (d = 20 мм), нагруженную изгибающей силой Р (рис. 95, а ), и треугольную ферму с одинаковым вылетом l, составленную из стержней того же диаметра.
Верхний стержень фермы под действием силы Р работает на растяжение, нижний — на сжатие. При соотношениях, показанных на рисунке, максимальное напряжение изгиба в балке в 550 раз больше напряжений растяжения-сжатия в стержнях фермы, а максимальная деформация (в точке приложения силы Р) больше в 9·10 3 раз.
Для того чтобы сделать системы равнопрочными , необходимо увеличить диаметр балки до 165 мм (рис. 95, б ). При этом масса балки (не считая заделочного участка) становится в 25 раз больше массы фермы, а максимальный прогиб оказывается в 2 раза больше прогиба фермы.
Для достижения одинаковой жесткости (равенство максимальных прогибов) необходимо увеличить диаметр балки до 200 мм (рис. 95, в ). Напряжения снижаются, составляя 0,6 от напряжения в стержнях фермы.
Связь между прогибом f б консольной балки круглого сечения в плоскости приложения силы и прогибом f ф ферменной системы при одинаковых сечениях можно выразить соотношением
где l — длина вылета; d — диаметр стержней балки и фермы; α — половина угла при вершине ферменного треугольника.
Отношение f б /f ф в функции угла α для различных значений l/d приведено на рис. 96, a .
При одинаковости сечений прогиб консольной балки может быть в сотни и тысячи раз больше прогиба ферменной системы. Разница резко возрастает с увеличением отношения l/d, т. е. относительным утонением стержней. Однако и для наиболее жестких стержней (l/d = 10) разница в пользу ферменной системы весьма велика.
Отношение f б /f ф имеет пологий максимум при α = 45—60°. В этом диапазоне фермы типа, приведенного на рис. 95, обладают наибольшей жесткостью. Напряжения (рис. 96, б ) в балке во много раз больше напряжений в стержнях (например, при α = 45° в 100—1000 раз).
Конструктивную аналогию системам, изображенным на рис. 95, представляет литой кронштейн (рис. 97).
Жесткость узлов соединения стержней в раскосном кронштейне видоизменяет условия их работы по сравнению с чистой фермой, в которой стержни соединены шарнирами; все же в случае раскосного кронштейна (рис. 97, б ) стержни работают преимущественно на растяжение-сжатие, тогда как балочный кронштейн (рис. 97, а ) подвергается изгибу. Конструкция становится еще более прочной и жесткой, если стержни кронштейна соединить сплошной перемычкой, связывающей их в жесткую систему (рис. 97, в ).
Кронштейн ферменного типа с вертикальным стержнем (рис. 97, г ) значительно менее жесткий, чем кронштейн на рис. 97, б , так как конец вертикального стержня под нагрузкой перемещается приблизительно по направлению действия силы и для ограничения деформаций его жесткость не используется.
В тонкостенном цилиндрическом отсеке, несущем поперечную нагрузку Р (рис. 98, а ), все участки, расположенные по образующим, подвергаются изгибу.
Нагрузку воспринимают преимущественно боковые стенки (рис. 98, б ), параллельные плоскости действия изгибающего момента (зачернены на рисунке), так как их жесткость в этом направлении во много раз больше жесткости стенок, расположенных перпендикулярно плоскости действия момента.
При конической форме (рис. 98, в , г ), приближающей конструкцию к ферменной (см. рис. 95), стенки конуса, расположенные в плоскости действия изгибающего момента, работают: верхние на растяжение, а нижние подобно раскосу — на сжатие. Боковые стенки испытывают преимущественно изгиб; их жесткость соизмерима с жесткостью верхних и нижних стенок. Следовательно, при конической форме стенки отсека полностью включаются в работу; прочность и жесткость конструкции увеличиваются. Связь между растянутыми и сжатыми стенками осуществляют кольца жесткости m, n, которые помимо силового замыкания предотвращают овализацию конуса под действием нагрузки. Такие кольца являются непременным условием правильной работы тонкостенных отсеков.
Близки к конусам по жесткости тюльпанные (рис. 98, д ), сферические (рис. 98, е ), тороидные (рис. 98, ж ) и аналогичные формы.
Пример устранения напряжений изгиба показан также на рис. 99.
Здесь двухопорная балка, подвергающаяся изгибу (рис. 99, а ), заменена более выгодной стержневой системой (рис. 99, б ), наклонные стержни которой работают на сжатие, а горизонтальные — на растяжение. Близка к этому случаю арочная балка (рис. 98, в ), работающая преимущественно на сжатие.
Связь между прогибом f б двухопорной балки в плоскости действия изгибающей силы и прогибом f ф стержневой (ферменной) системы по рис. 99, б можно выразить соотношением
где l — пролет балки; d — диаметр балки (и стержней ферменной системы); α — боковой угол треугольника фермы.
Отношение f б /f ф показано на графике (рис. 100, а ) в функции угла α для различных значений l/d.
График свидетельствует о большом преимуществе системы, работающей на сжатие, перед системой, испытывающей изгиб. Прогиб балки в плоскости действия нагрузки в сотни и тысячи раз превышает прогиб стержневых систем. Даже при малых значениях угла (α ≈ 15°) прогиб стержневой системы, например, при l/d = 50, в 200 раз меньше прогиба системы, работающей на изгиб.
Как и в предыдущем случае (см. рис. 96, а ), стержневая система имеет наибольшую жесткость при α = 45—60°.
Из графика на рис. 100, б следует, что напряжения в балке в 30—300 раз больше напряжений в стержнях фермы. При больших значениях l/d у стержней, работающих на сжатие, возникает опасность появления продольного изгиба. Это обстоятельство следует учитывать при конструировании стержневых систем.
На рис. 101, а показан случай нагружения цилиндра осевой силой.
Нагрузка вызывает прогиб днища цилиндра, передающийся обечайке через пояс сопряжения обечайки с днищем (деформации показаны штриховой линией). Система является нежесткой. При замене цилиндра конусом (рис. 101, б ) система по основной схеме восприятия сил приближается к стержневой ферме, изображенной на рис. 99, б . Стенки конуса работают преимущественно на сжатие; роль стержня, воспринимающего распор, в данном случае выполняют жесткие кольцевые сечения конуса, ограничивающие радиальные деформации стенок.
Наибольшей жесткостью при наименьшей массе обладают конусы с углом при вершине 60—90°.
Повышенную жесткость имеют сферическая, яйцевидная и тому подобные формы (рис. 101, в и г ).
На рис. 101, д —з приведены примеры жестких конструкций. Как и в случае конуса (см. рис. 98), работающего на изгиб, существенное условие повышения жесткости и прочности здесь состоит в придании деталям кольцевых поясов жесткости, из которых верхний m работает на сжатие, а нижний n — на растяжение.
В усиленных конструкциях (рис. 101, и —м ) введены элементы, непосредственно воспринимающие силу сжатия: ребра, цилиндры и конусы.
В общей постановке вопроса задача увеличения жесткости заключается в том, чтобы найти точки наибольших перемещений системы, деформируемой под действием нагрузки, и предотвратить эти перемещения введением элементов растяжения-сжатия, расположенных по направлению перемещений. Классическим примером решения этой задачи является увеличение жесткости рам и ферменных конструкций раскосами.
Жесткость стержневой рамы, подвергающейся действию сдвигающих сил Р (рис. 102, а ), крайне незначительна и определяется только сопротивлением вертикальных стержней изгибу и жесткостью узлов соединения стержней.
Введение косынок (рис. 102, б ) приближает схему нагружения стержней к схеме работы заделанных балок и несколько уменьшает деформации.
Наиболее эффективно введение диагональных связей (раскосов), подвергающихся растяжению или сжатию. Раскос растяжения (рис. 102, в ) должен при перекосе рамы удлиниться на величину Δ. Так как жесткость растягиваемого стержня во много раз больше изгибной жесткости вертикальных стержней, то общая жесткость системы резко возрастает. Аналогично действует раскос сжатия (рис. 102, г ). Но в этом случае необходимо считаться с возможностью продольного изгиба сжатого стержня, что делает систему менее желательной.
Если нагрузка действует попеременно в обоих направлениях, то применяют раскосы перекрестные или чередующегося направления (рис. 102, д и е ).
В порядке возрастающей жесткости на рис. 103, а —и представлены схемы плоских ферм и на рис. 103, к —н — сложных плоских ферм с усиливающими элементами, предотвращающими продольный изгиб и потерю устойчивости стержней.
На рис. 104, а показана схема деформации стенок цилиндрического резервуара, подвергающегося действию внутреннего давления. Участки наибольших деформаций целесообразно связать элементами, работающими на растяжение: обечайку — кольцом 1, днища — анкерным болтом 2 (рис. 104, б ).
Консольные и двухопорные системы
Если по конструкции и функциональному назначению детали нельзя избежать изгиба, то на первый план выступает задача уменьшения деформаций и напряжений изгиба.
На рис. 105 изображены основные схемы изгиба балок: консольной (а ) опертой по концам (б ) и с заделанными концами (в ).
Из сопоставления максимальных изгибающих моментов и прогибов видно большое преимущество двухопорных балок перед консольной по жесткости и прочности. При одинаковых длине, сечении балок и нагрузке максимальный изгибающий момент (а, следовательно, и максимальные напряжения изгиба) в двухопорной балке в 4 раза, а в двухопорной (заделанной) в 8 раз меньше, чем в консольной. Еще больше преимущества по жесткости. Максимальный прогиб двухопорной балки в 16 раз, а двухопорной заделанной в 64 раза меньше, чем консольной. Практически различие между двухопорными и консольными деталями выражено не так резко, как в приведенном схематическом сравнении. В сравнимых конструктивных вариантах консольной и двухопорной балок длина консоли редко бывает равной расстоянию между опорами в двухопорной балке; чаше всего она значительно меньше.
В консольной (г ) и двухопорной (д ) установке вала-шестерни по габаритным условиям расстояние между опорами в двухопорной установке не удается сделать меньшим 2l, вследствие чего оба варианта приходится сравнивать на базе различных, а не одинаковых, как в предыдущем случае, длин.
Максимальный изгибающий момент при двухопорной установке в 2 раза меньше, чем в консольной. Выигрыш в максимальных напряжениях изгиба гораздо больше, потому что момент сопротивления в опасном сечении (в плоскости действия силы Р) двухопорного вала значительно больше момента сопротивления в опасном сечении (в плоскости переднего, ближайшего к нагрузке подшипника) консольного вала. При соотношениях, приведенных под рис. 105, напряжения в опасном сечении двухопорного вала в 5 раз меньше, чем в консоли.
Максимальный прогиб двухопорного вала формально в 2 раза меньше прогиба консольного вала, а если учесть больший момент инерции I" сечения двухопорного вала по сравнению с моментом инерции I консольного вала, то фактически еще меньше (при соотношениях, приведенных под рисунком, — в 6,5 раза).
Нагрузка на подшипники двухопорного вала меньше нагрузки на передний подшипник консольного вала Р(1+l/L) в 2(1+l/L) раза.
Еще благоприятнее соотношения для двухопорного вала с заделанными концами. Реальное приближение к этому случаю можно получить увеличением жесткости опор, например, применением роликовых подшипников и усилением стенок корпуса (рис. 105, е ). В данном случае максимальный изгибающий момент меньше в 4 раза по сравнению с консолью и в 2 раза по сравнению с двухопорным валом, установленным на шарикоподшипниках. Максимальный прогиб вала на жестких опорах соответственно меньше в 8 и 4 раза (без учета различия величин I и I").
Однако при коротких и жестких валах повышение жесткости опор практически не дает выгоды, так как жесткость вала стирает разницу между схемами валов свободно опертого и с заделанными концами.
Увеличение жесткости и прочности консольных конструкций
Если применение консольной установки продиктовано необходимостью, то следует принимать все меры к устранению присущих ей недостатков. Необходимо всемерно уменьшать вылет консоли, увеличивать жесткость и прочность консольной части конструкции.
На рис. 106 приведены нецелесообразная (а ) и улучшенная (б ) конструкции консольного вала, в которой длина l" консоли уменьшена до предела, допустимого конструкцией; момент инерции и момент сопротивления консоли на наиболее нагруженных участках увеличены. Передний подшипник, воспринимающий повышенную нагрузку, усилен.
Распространенным случаем консоли в машиностроении являются опорные буртики цилиндрических деталей. В нерациональной конструкции (рис. 106, в ) буртик имеет чрезмерный вылет. Если вылет уменьшить, например, в 3 раза (рис. 106, г ), то во столько же раз уменьшаются напряжения изгиба в опасном сечении; максимальная деформация снижается в 27 раз.
В планетарной передаче (рис. 106, д ) консольные пальцы 1 сателлитов подвергаются изгибу центробежной силой сателлитов Р цб и окружными силами привода Р окр. Соединение пальцев дисками 2 (рис. 106, е ) устраняет консольный изгиб только от сил Р цб. Окружные силы по-прежнему консольно изгибают пальцы.
В рациональной конструкции (рис. 106, ж ) несущий диск 3 привернут к лапам m диска водила, которые воспринимают окружные силы, полностью разгружая пальцы от изгиба.
В ряде случаев можно добиться значительного укорочения консоли изменением формы детали. Вылет насадного конического колеса (рис. 107, а ) можно уменьшить, переменив положение ступицы относительно венца (рис. 107, б ) или изменив конструкцию колеса, выполняя его заодно с валом (рис. 107, в ).
Нагрузка на переднюю опору консоли (рис. 108, a ) N 1 = Р(1 + l/L), на заднюю — N 2 = Pl/L, где Р — сила, действующая на консоль; l — длина консоли; L — расстояние между опорами.
На рис. 109, а даны безразмерные отношения N 1 /P и N 2 /P в функции L/l. Как видно, нагрузки на опоры резко возрастают с уменьшением расстояния между опорами. С увеличением отношения L/l нагрузки падают, причем N 1 асимптотически стремится к величине Р, а N 2 — к нулю. При L/l > 2—2,5 нагрузки становятся практически постоянными, а при L/l < 1 резко возрастают. Таким образом, целесообразный диапазон отношений L/l заключен в пределах 1,5—2,5 (заштрихованная область).
В качестве общего правила можно принять, что расстояние между опорами должно быть равно удвоенной консоли. При этом нагрузка на переднюю опору N 1 = 1,5Р. Разумеется за большими отношениями L/l остается преимущество более точной фиксации вала.
На том же графике изображено отношение нагрузок на переднюю и заднюю опоры N 1 /N 2 = 1 + L/l, которым можно руководствоваться при выборе подшипников в тех случаях, когда желательно получить их равную долговечность. Для рекомендуемого значения L/l = 2 величина N 1 /N 2 = 3. Из основной формулы расчета подшипников качения L = (C/P) α вытекает, что для соблюдения равной долговечности L динамическая грузоподъемность С переднего и заднего подшипников должна находится в отношении С 1 /С 2 = 3.
При системе обратной консоли детали, насаженной на вал, придают колоколообразную форму (см. рис. 108, б ) с таким расчетом, чтобы нагрузка действовала в пролете между опорами. При достаточной жесткости системы можно принять схему распределения нагрузок, приведенную на рис. 109, б . Нагрузки на опоры показаны на этом графике в виде безразмерных отношений N 1 /Р и N 2 /P в функции А/L (А — расстояние от задней опоры до плоскости действия силы Р). Область обратной консоли заключена в пределах значений А/L = 0—1; при значениях A/L > 1 имеет место прямая консольность.
Максимальные значения N 1 и N 2 в области обратной консоли равны действующей силе P (отношения N 1 /P и N 2 /P равны единице). Нагрузки N 1 и N 2 имеют одинаковое и максимальное значение 0,5P при A/L = 0,5, когда плоскость действия силы P находится посередине пролета между опорами.
Для полного устранения консоли деталь монтируют на неподвижной опоре 1 (см. рис. 108, в ), через которую проходит приводной валик 2, разгруженным от изгиба и передающий детали крутящий момент через шлицевой венец. Здесь подшипники нагружены так же, как у двухопорного вала. Однако они работают в менее благоприятных условиях, так как у них вращается наружное кольцо (а не внутреннее как в случае двухопорного вала), вследствие чего их долговечность уменьшается.
Из сказанного о недостатках консольных систем отнюдь не вытекает, что конструктор должен безусловно избегать применения консолей. Консольные системы являются вполне закономерным элементом конструирования и широко используются на практике. Необходимо только знать их особенности и устранять недостатки соответствующими конструктивными мерами.
Применение консолей часто обеспечивает более простые, компактные, технологические и удобные для сборки конструкции, чем двухопорные установки. В качестве примера на рис. 110 показана конструкция центробежного насоса с двухопорной (а ) и консольной (б ) установкой вала крыльчатки.
В консольном варианте упрощается сборка, облегчается подход к крыльчатке и гидравлической полости насоса, улучшается вход рабочей жидкости на крыльчатку, устраняется одно уплотнение, улучшается центрирование вала. Опоры вала расположены в одной корпусной детали, посадочные отверстия под опоры можно точно обработать с одной установки.
В двухопорном варианте опоры центрируются одна относительно другой через стык корпусных деталей, которые по конструкции узла можно зафиксировать один относительно другого только контрольными штифтами; совместная обработка посадочных отверстий затруднительна.
В целом агрегат в консольном исполнении сильно выигрывает по простоте, точности изготовления, надежности и удобству эксплуатации.
Жесткость и прочность консолей в большой степени зависят от условий заделки в корпусе. Усиление консоли как таковой бесполезно, если узел заделки недостаточно жесткий (рис. 111, а ).
При радиальной заделке консоли придают фланец, который притягивают болтами к припадочной плоскости, усиленной ребрами m (рис. 111, б ).
В системе осевой заделки (рис. 111, в ) консоли придают хвостовик, диаметром примерно равным диаметру консоли, который крепят запрессовкой или затяжкой в бобышке, жестко связанной с корпусом ребрами или (как показано на рисунке) коробкой. Для устойчивого крепления длину заделки делают не менее диаметра консоли.
В наиболее жесткой системе радиально-осевой заделки консоль крепят одновременно на фланце и на хвостовике, который сажают в бобышке по посадке с натягом или затягивают гайкой (рис. 111, г и д ).
Рациональное расположение опор
Так как прогиб двухопорной балки пропорционален третьей степени пролета, то сближение опор является весьма эффективным средством повышения жесткости. На рис. 112, а показана двухопорная установка зубчатого колеса. При диаметре вала 40 мм, длине 200 мм и нагрузке 10 кН прогиб вала в конструкции а относительно большой (~0,1 мм), влияющий на работу зубьев колес.
Если расстояние между опорами сократить, например, в 3 раза (рис. 112, б ), то максимальные изгибающий момент и напряжения в вале уменьшаются также в 3 раза, а максимальный прогиб — в 27 раз. В связи с уменьшением пролета, а также увеличением момента инерции работающего участка вала прогиб становится пренебрежимо малым.
Во многих случаях жесткость системы удается увеличить введением дополнительных опор (рис. 113). В конструкции а коленчатый вал оперт в трех подшипниках. Система имеет малую жесткость; для ее увеличения щекам и шейкам вала необходимо придать большие сечения. Жесткость резко увеличивается при введении опор между каждым коленом. Последняя конструкция б применяется почти всегда.
На рис. 114 показаны приемы увеличения жесткости и прочности узла крепления шатуна в вилке. Так как шатун совершает относительно вилки колебательное движение, обычно небольшой амплитуды, то в данном случае можно ввести дополнительные опоры, практически полностью устраняющие изгиб. Исходная, часто применяемая конструкция а , в которой палец работает на изгиб, обладает малой жесткостью. В конструкции б палец разгружен от изгиба путем его упора в ножку 1, выполненную в вилке.
Изгиб резко уменьшается при увеличении длины верхней несущей поверхности шатуна (конструкции в , г ). На участках h палец работает на сжатие. Так как деформации при сжатии ничтожно малы по сравнению с деформациями изгиба, практически вся нагрузка воспринимается сжатием пальца.
В конструкциях, предназначенных для восприятия нагрузки в обоих направлениях с большой амплитудой колебательного движения, упрочнения достигают увеличением числа опор и уменьшением пролетов, подвергающихся изгибу. В конструкции д вследствие сокращения вдвое плеча l" действия сил напряжения изгиба уменьшаются в 2 раза, а деформации — в 8 раз по сравнению с исходной конструкцией а . С увеличением числа опор (конструкция е ) схема нагружения приближается к чистому сдвигу. Изменение вида и деформации и увеличение числа сечений, участвующих в передаче нагрузки, значительно увеличивают прочность и жесткость узла.
В некоторых случаях при нагрузке одностороннего действия возможна прямая передача сил на опоры с полной разгрузкой пальца (конструкции ж , з ). Необходима точная обработка по цилиндру опорных поверхностей m соосно с опорными поверхностями пальца, иначе схема восприятия сил становится неопределенной.
Рациональные сечения
Для повышения жесткости без увеличения массы деталей необходимо усиливать участки сечений, подвергающиеся при данном виде нагружения наиболее высоким напряжениям, и удалять ненагруженные и малонагруженные участки. При изгибе напряжены сечения, наиболее удаленные от нейтральной оси. При кручении напряжены внешние волокна: по направлению к центру напряжения уменьшаются, и в центре они равны нулю. Следовательно, целесообразно всемерно развивать наружные размеры, сосредотачивая материал на периферии и удаляя его из центра.
Наибольшей жесткостью и прочностью при наименьшей массе обладают развитые по периферии полые тонкостенные детали тина коробок, труб и оболочек.
В табл. 21 приведено сравнение показателей различных профилей при изгибе.
В основу сравнения положены условия равенства масс (сечений F) и прочности (моментов сопротивления W). Увеличение прочности и жесткости достигается последовательным применением принципа разноса материала в область действия наибольших напряжений. За единицу приняты масса, моменты сопротивления и инерции исходного профиля 1, у которого материал сосредоточен вблизи нейтральной оси.
Придание наиболее целесообразной двутавровой формы профилям одинаковой массы (эскизы 1—5) увеличивает их прочность в 9—12 раз, а жесткость — в 40—70 раз по сравнению с исходным профилем. Для профилей, одинаковых с исходным профилем прочности (эскизы 6—9), придание двутавровой формы снижает массу до 0,2—0,12 и повышает жесткость в 3—3,5 раза по сравнению с исходным профилем.
Зависимость между массой, прочностью и жесткостью цилиндрических валов с разным отношением d/D приведена на рис. .
В качестве конструктивного примера в табл. 22 представлен вал зубчатого колеса, установленный на подшипниках качения, и приведены сравнительные показатели жесткости (I), прочности (W), массы (m), удельной прочности (W/m) и долговечности (L h) подшипников при последовательном увеличении диаметра вала (и размера подшипников). За единицу приняты показатели массивного вала.
Повышение поперечной жесткости . С увеличением наружных размеров деталей и уменьшением толщины их стенок необходимо во избежание местных деформаций повышение жесткости в направлении, поперечном действию изгибающих моментов.
Для цилиндрических валов эту задачу решают введением поясов и перемычек жесткости (рис. 115, а , б ) в плоскости действия нагрузок, на опорных и заделочных участках, а также на свободных концах детали (рис. 115, в , г ).
На рис. 116 показано усиление балок поперечными ребрами 1, коробками 2, полукруглыми накладками 3, косыми связями 4, 5.
При изгибе корытного профиля (рис. 117, 1 потеря устойчивости наступает в результате деформации вертикальных стенок (в направлениях, указанных стрелками).
Устойчивость профиля можно повысить созданием узлов жесткости на участках перехода стенок в горизонтальную полку посредством продольных 2 или местных 3 и 4 выемок, а также ребер 5. Сопротивление стенок деформации повышают ребрами 6 и гофрами 7. Связь между стенками и полкой можно увеличить также усилением полки ребрами 8—10 и сотами 11.
На рис. 117 показаны способы одновременного усиления полки и стенок (12; 13). Эффективное средство увеличения устойчивости профиля — блокирование деформаций поперечными перегородками 14—18, анкерными болтами 19 и пластинами 20. Наибольшей жесткостью обладают закрытые профили 21; 22, особенно с поперечными 23 или продольными диагональными 24 связями.
При изгибе и кручении профилей особенно эффективны продольные диагональные связи (табл. 23). Достаточно одной диагональной связи; вторая связь увеличивает жесткость незначительно.
Оребрение
Для увеличения жесткости, особенно литых корпусных деталей, широко применяют оребрение. Однако при этом необходимо соблюдать осторожность, так как неправильное соотношение сечений ребер и оребряемой детали может вместо упрочнения привести к ослаблению.
У деталей, подвергающихся изгибу в плоскости расположения наружных ребер (рис. 118, а ), на вершине ребра возникают напряжения растяжения, достигающие большого значения вследствие малой ширины и малого сечения ребра.
Особенно опасны тонкие ребра, суживающиеся к вершине (рис. 118, б , в ); разрушение стали всегда начинается с разрыва вершины ребер. Прочность значительно возрастает при утолщении ребер, особенно на опасном участке, т. е. у вершины (рис. 118, г и д ).
Ослабление детали ребрами формально выражается в уменьшении момента сопротивления сечения детали. Сравним прочность и жесткость профиля прямоугольного сечения (рис. 119, а ) и того же профиля с ребром (рис. 119, б ).
Можно показать, что отношение моментов инерции J и J 0 оребренного и исходного профиля
где η = h/h 0 — отношение высоты ребра h к высоте h 0 исходного профиля; δ = b/b 0 — отношение ширины ребра b к ширине b 0 исходного профиля.
Для сечения с рядом параллельных ребер (рис. 119, в ) величина b 0 представляет собой шаг ребер (b 0 = t).
Относительный шаг t 0 = b 0 /b = 1/δ. Отношение моментов сопротивления сравниваемых профилей
С учетом формул (54) и (55) построены графики (рис. 120), покатывающие влияние η и t 0 на J/J 0 и W/W 0 . Введение ребер во всех случаях увеличивает момент инерции сечения и, следовательно, жесткость детали на изгиб и тем резче, чем выше ребра и больше их относительная толщина.
Иная картина получается для моментов сопротивления. Введение ребер, сечение которых мало по сравнению с сечением оребряемой детали (малые значения η, большой шаг t 0), уменьшает момент сопротивления, т. е. ослабляет деталь. Момент сопротивления в неблагоприятном случае (η = 2; t 0 = 100) уменьшается в 3 раза по сравнению с исходным профилем. Как это ни кажется парадоксальным, удаление таких ребер упрочняет деталь.
Добиться повышения прочности можно увеличением высоты ребер. Ребра с относительной высотой η > 7 не уменьшают прочности детали вплоть до самых больших значений относительного шага, какие могут встретиться на практике (t 0 = 100). Однако у литых деталей высота ребер ограничивается технологией литья. Относительную высоту ребер на практике редко делают больше η = 5. Условия литья ограничивают также толщину ребер; обычно ее делают не более (0,6—0,8)·h 0 .
Реальнее другой путь — уменьшение относительного шага. При t 0 < 5 не наступает ослабления даже при самых низких ребрах (η < 1). Значения шагов, не вызывающих ослабления детали, можно определить по сетке кривых t 0 (рис. 120, б ), возводя перпендикуляры из заданных величин η на оси абсцисс до пересечения с линией W/W 0 = 1.
Для практического определения максимально допустимого шага можно исходить из соотношения
(где b — толщина ребер в мм), выражающего осредненные значения t при W/W 0 = 1,5—2.
На основании этой формулы составлен график (рис. 121), позволяющий найти допустимые по прочности параметры оребрения.
1. Пусть толщина ребра b = 5 мм; η = 2 По графику (штриховые линии) находим максимально допустимый шаг t = 40 мм.
2. Пусть шаг ребер t = 100 мм; b = 8 мм. Согласно графику, минимальное допустимое значение η = 2,5.
Выведенные соотношения формально действительны для ребер, испытывающих при изгибе как растяжение (рис. 122, а ), так и сжатие (рис. 122, б ).
На самом деле сжатые ребра гораздо прочнее, так как почти все литейные материалы (за исключением сплавов Mg) значительно лучше сопротивляются сжатию, чем растяжению. Поэтому приведенные рекомендации имеют преимущественное значение для растянутых ребер.
Ребра треугольной формы . Очень часто применяют ребра треугольной формы с высотой, уменьшающейся в плоскости действия изгибающего момента. При такой форме ребер, какую бы начальную высоту они не имели, неизбежен участок, где наступает ослабление детали.
На рис. 123 приведены формы треугольных ребер для случая консольной детали, изгибаемой силой, приложенной на конце консоли. Под каждой фигурой показана картина изменения момента сопротивления W и напряжений изгиба σ вдоль оси детали. Для моментов сопротивления за единицу принят момент сопротивления W 0 неоребренной части детали; для напряжений — напряжение σ 0 на участке сопряжения консоли с фланцем. Напряжения для неоребренной детали показаны штриховой линией.
При форме ребра, показанной на рис. 123, а , ослабление наступает на участке m сопряжения ребра со стенкой консоли. Такая форма ребра особенно невыгодна потому, что ослабление приходится на область больших значений изгибающего момента и на ослабленном участке возникает резкий скачок напряжений. Благоприятно действует удлиненное ребро (рис. 123, б ).
Ослабленное сечение m смещается в область меньшего изгибающего момента. Напряжения на ослабленном участке несколько превышают максимальные напряжения в детали. Если ребро доходит до конца консоли (рис. 123, в ), то ослабление приходится на область минимальных значений изгибающего момента и почти не сказывается на напряжениях.
Оребрение коробчатых деталей . Соотношения, выведенные в предыдущих разделах, справедливы для профилей прямоугольного сечения (детали типа плит). У коробчатых деталей влияние ребер на жесткость и прочность гораздо слабее вследствие относительно больших моментов инерции и сопротивления коробки. Разберем пример коробчатой детали квадратного сечения с ребрами, расположенными в плоскости действия изгибающего момента (рис. 124, а ).
Отношение момента инерции J оребренного профиля к моменту инерции J 0 исходного профиля (на рисунке заштрихован)
где а = В 1 /В — отношение сторон внутреннего и внешнего квадратов; η = h/s — отношение высоты h ребра к толщине стенки s = 0,5В (1—а ); ϰ = b/s — отношение толщины b ребра к толщине стенки s; z — число ребер.
Эти соотношения показаны на рис. 125, а , б в функции η (приняты типичные для литых деталей величины а = 0,95; ϰ = 0,6).
Введение ребер повышает жесткость детали при любых значениях η, но менее заметно, чем в случае профиля прямоугольного сечения (см. рис. 120, а ). Введение редко расставленных ребер (z = 1—2) снижает прочность детали до 0,8—0,9 исходного значения, т. е. менее существенно, чем в случае прямоугольного профиля (см. рис. 120, б ). При z > 3 прочность возрастает. Для повышения прочности на 20—25% необходимо при обычных для литых деталей значениях η = 3—4 (заштрихованная область) введение 7—10 ребер.
При консольном нагружении верхние ребра m (см. рис. 124, а ) работают на растяжение, нижние n — на сжатие, а при нагружении по схеме двухопорной балки — наоборот. Напряжения растяжения имеют в том и другом случае наибольшее значение в вершинах ребер, сопротивление которых разрыву и лимитирует прочность детали.
В случае внутренних ребер (см. рис. 124, б ) изменение жесткости и прочности выражается равенством
Это выражение в функции η изображено на рис. 125, в ; введение внутренних ребер во всех случаях увеличивает и жесткость, и прочность детали, хотя жесткость повышается несколько слабее, чем в случае наружных ребер (см. рис. 125, а ). Для увеличения прочности на 20—25% достаточно введения 5—7 ребер с относительной высотой η = 3—4 (заштрихованная область).
При консольном нагружении верхние ребра р (см. рис. 124, б ) работают на сжатие, нижние q — на растяжение, а при нагружении по схеме двухопорной балки - наоборот. Напряжения растяжения в вершинах ребер вследствие меньшего расстояния от нейтральной оси значительно ниже, чем в случае наружных ребер.
Если изгибающая сила направлена в одну сторону, то можно нагрузить на сжатие верхние и нижние ребра сочетанием внутреннего и наружного оребрения. При консольном нагружении целесообразно расположение ребер по схеме на рис. 124, в , а при нагружении по схеме двухопорной балки — обратное. Несмотря на формальное уменьшение момента сопротивления по сравнению со схемой рис. 124, а , нагружаемость конструкции возрастает благодаря повышенной сопротивляемости ребер сжатию.
Наибольшее повышение жесткости и прочности достигается при увеличении высоты Н сечения до размера, определяемого вершинами ребер (см. рис. 124, г ). Изменение W/W 0 при этой схеме представлено на рис. 125, а . Прочность профиля с внутренними ребрами (η = 3—4) повышается по сравнению с исходным квадратным профилем в 1,3—1,7 раза соответственно при z = 1—10.
Таким образом, внутреннее оребрение во всех отношениях выгоднее наружного. При любых параметрах оребрения внутренние ребра увеличивают момент сопротивления изгибу. Прочность ребер на разрыв не лимитирует прочности конструкции. В тех же габаритных размерах, определяемых в случае наружного оребрения контурами вершин ребер, можно увеличить размеры коробки с выигрышем в жесткости и прочности конструкции. Наконец, внутреннее оребрение улучшает внешний вид и облегчает уход за машиной.
Правила конструирования . При конструировании ребер рекомендуется:
- избегать нагружения ребер на растяжение; применять во всех случаях, когда это допускает конструкция, ребра сжатия;
- избегать (особенно при ребрах растяжения) низких, тонких и редко расставленных ребер, снижающих прочность детали;
- в корпусных деталях применять внутреннее оребрение (за исключением особых случаев, например, когда наружные ребра необходимы для охлаждения летали);
- подводить ребра к узлам жесткости (рис. 126, а , б ), в частности к точкам расположения крепежных болтов (рис. 126, в , г );
- избегать ребер s криволинейного очертания, испытывающих при растяжении дополнительный изгиб; применять прямые ребра t.
Целесообразно (особенно у ребер растяжения) утолщать вершины, в которых при изгибе возникают наиболее высокие напряжения.
Оребрение деталей, подвергающихся кручению . При нагружении цилиндрических и близких к ним по форме деталей крутящим моментом продольные прямые ребра 1 крайне незначительно увеличивают жесткость детали (рис. 127).
Скорее такие ребра вредны, так как они подвергаются изгибу (в плоскости, перпендикулярной грани ребер), вызывающему в них повышенные напряжения. При одностороннем кручении выгодно применять косые ребра 2, которые под действием крутящего момента работают на сжатие, сильно увеличивая жесткость детали (частный случай применения принципа раскосных связей)
При крутящем моменте переменного направления целесообразно располагать ребра змейкой (3) или крестообразно (4). Косые и спиральные ребра менее подвержены внутренним напряжениям, возникающим при усадке в результате неравномерною охлаждения отливки. Однако формовка косых ребер на наружных цилиндрических, конических и тому подобных поверхностях затруднительна.
Для деталей цилиндрической и близкой к ней формы, работающих на кручение, целесообразно, как и в случае изгиба, применять внутреннее оребрение.
Кольцевые ребра применяют наряду с обычными прямыми ребрами для увеличения жесткости круглых деталей типа дисков, днищ цилиндров и др. Механизм их действия своеобразен. Предположим, что круглая пластина с кольцевым ребром изгибается приложенной в центре осевой силой Р (рис. 128, а ).
Деформации пластины передаются кольцу ребра, его стенки стремятся разойтись к периферии (рис. 128, б ). В кольце возникают напряжения растяжения, сдерживающие прогиб пластины. Кольцевое ребро, обращенное навстречу нагрузке (рис. 128, в ) действует аналогично, с той лишь разницей, что оно подвергается сжатию в радиальных направлениях.
Для повышения жесткости выгодно увеличивать высоту кольцевых ребер и располагать их на радиусе, где угол прогиба пластины имеет наибольшее значение; для пластин, опертых по краям, — ближе к периферии; для пластин с заделанными краями — ближе к их среднему радиусу. Расположение ребер на небольшом расстоянии от центра пластины почта бесполезно. Значительно повышает жесткость и прочность конструкции введение лучевых связей, сдерживающих радиальную деформацию кольцевых ребер (рис. 128, г —е ).
Разновидности ребер . Для придания деталям особо высокой жесткости применяют ребра (рис. 129): вафельные 1, шахматные 2, сотовые 3 и ромбические 4.
Полые ребра (рис. 130), представляющие собой рельефы открытого 1—8 или закрытого 9—11 профиля, в отличие от обычных ребер во всех случаях увеличивают наряду с жесткостью и прочность конструкции.
Ребра закрытого типа жестче открытых, но их формовка затруднительна. Практически такие же результаты по жесткости дают открытые ребра, усиленные поперечными перегородками 4—6; 8.
Внутренние полые ребра 11 предпочтительнее наружных. В случае, когда внутренние замкнутые ребра, имеющие прямоугольный профиль, соединяются одно с другим, получается наиболее жесткая и прочная коробчатая двустенная конструкция 12.
Конструктивные примеры . На рис. 131 приведены примеры неправильной и правильной конструкции ребер.
Корпусная деталь 1 с работающим на растяжение ребром m на участке перехода двух сечений весьма невыгодна по прочности. Удаление ребра увеличивает прочность детали 2. Если вводить ребро, то ему следует придать тавровое сечение 3 или расположить так, чтобы оно работало на сжатие 4. На рис. 131 изображены отсеки цилиндрической корпусной детали с перегородкой (диафрагмой), нагруженной поперечной силой Р или изгибающим моментом М.
Короткие ребра 5, 6 ослабляют перегородку на участках n. Лучше конструкции с ребрами постоянной высоты 7 или расширяющимися к месту заделки 8. Наибольшей прочностью обладают конструкции с гофрированной перегородкой 9 и коробчатые 10, особенно усиленные внутренними поперечными ребрами. Консольная корпусная деталь 11 имеет сферическую форму. Редко расставленные ребра небольшой высоты ослабляют деталь. Удаление ребер увеличивает прочность, особенно если стенки 12 расширены в пределах располагаемых габаритов. Дальнейшего упрочнения можно достичь внутренним оребрением продольными 13 или вафельными 14 ребрами. Высокой прочностью и жесткостью обладает деталь 15 с гофрированными стенками.